
Quality Control System, Compensation Plan, Digitalization.
Four numbers at a glance
-
0.45% Quality Complaint Rate
-
Quality Issue Response in 24h
-
9.4/10 Dispute resolution satisfaction rating
-
97% Third-party Inspection Pass Rate
A Comprehensive Quality Control System

Professional Training for Quality Inspectors Team
Skylore Chain have an experienced quality inspection team whose members have years of hands-on experience in their respective fields and have undergone systematic training to master the latest quality management standards and advanced inspection techniques. From raw material inspection to finished product shipment, they meticulously control each stage to ensure product quality consistently meets customer requirements and industry standards.

Multiple Quality Inspection Stages Ensure Product Consistency
Skylore Chain have a comprehensive and rigorous quality inspection process that covers every stage, from supplier selection and raw material inspection to production process control, finished product testing, and packaging checks. Multiple inspections and data traceability ensure product consistency and high quality. In addition, we collaborate with third-party quality inspection agencies to enhance transparency and impartiality, ensuring compliance with international and customer standards.
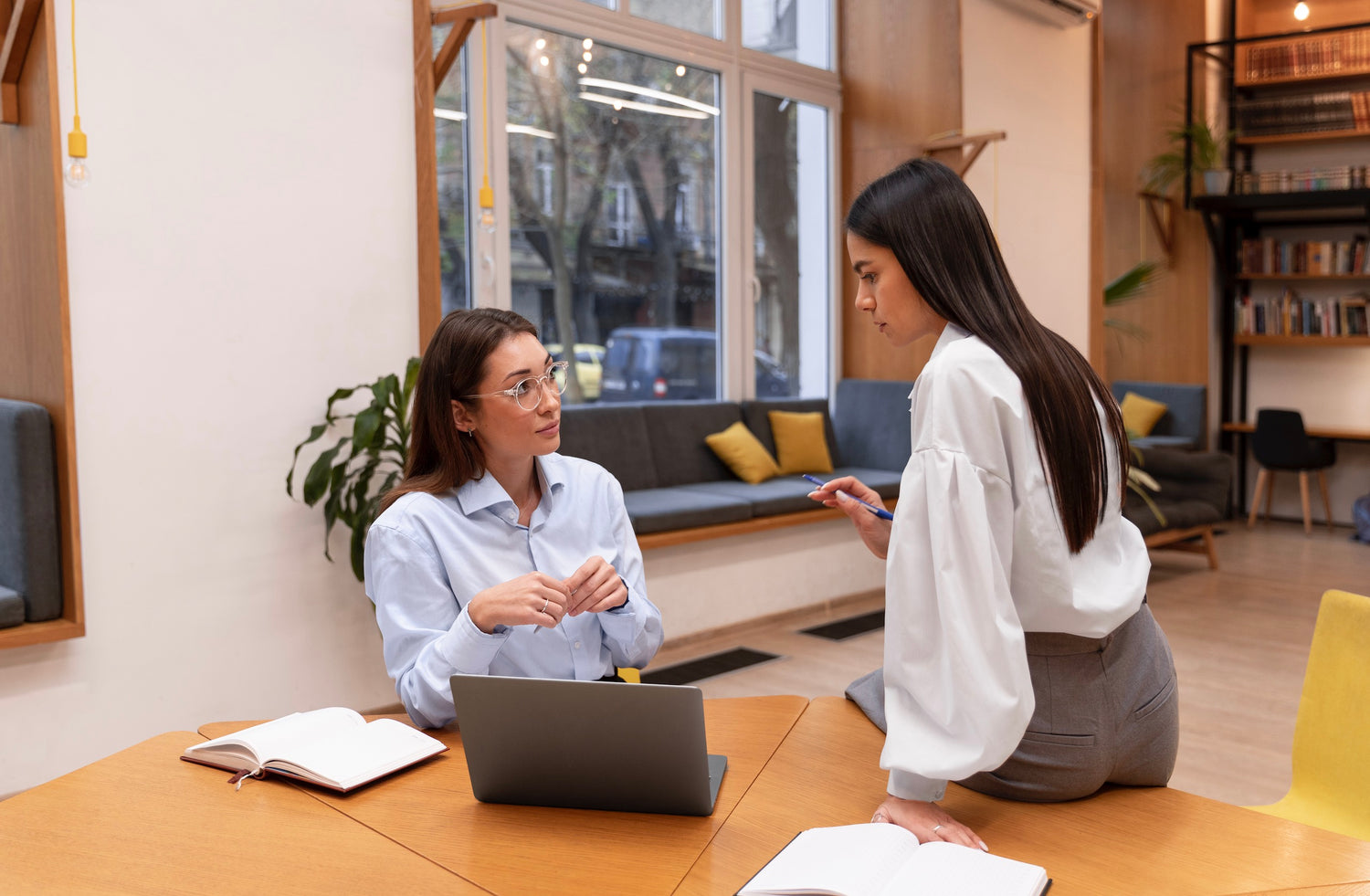
Client-customized Quality Inspection Standards.
Skylore Chain offer customized quality inspection standards to meet the unique needs of different clients. Depending on the product type, market requirements, and quality expectations, we can flexibly adjust the inspection process and standards, including specific testing items, sampling ratios, and acceptance criteria.
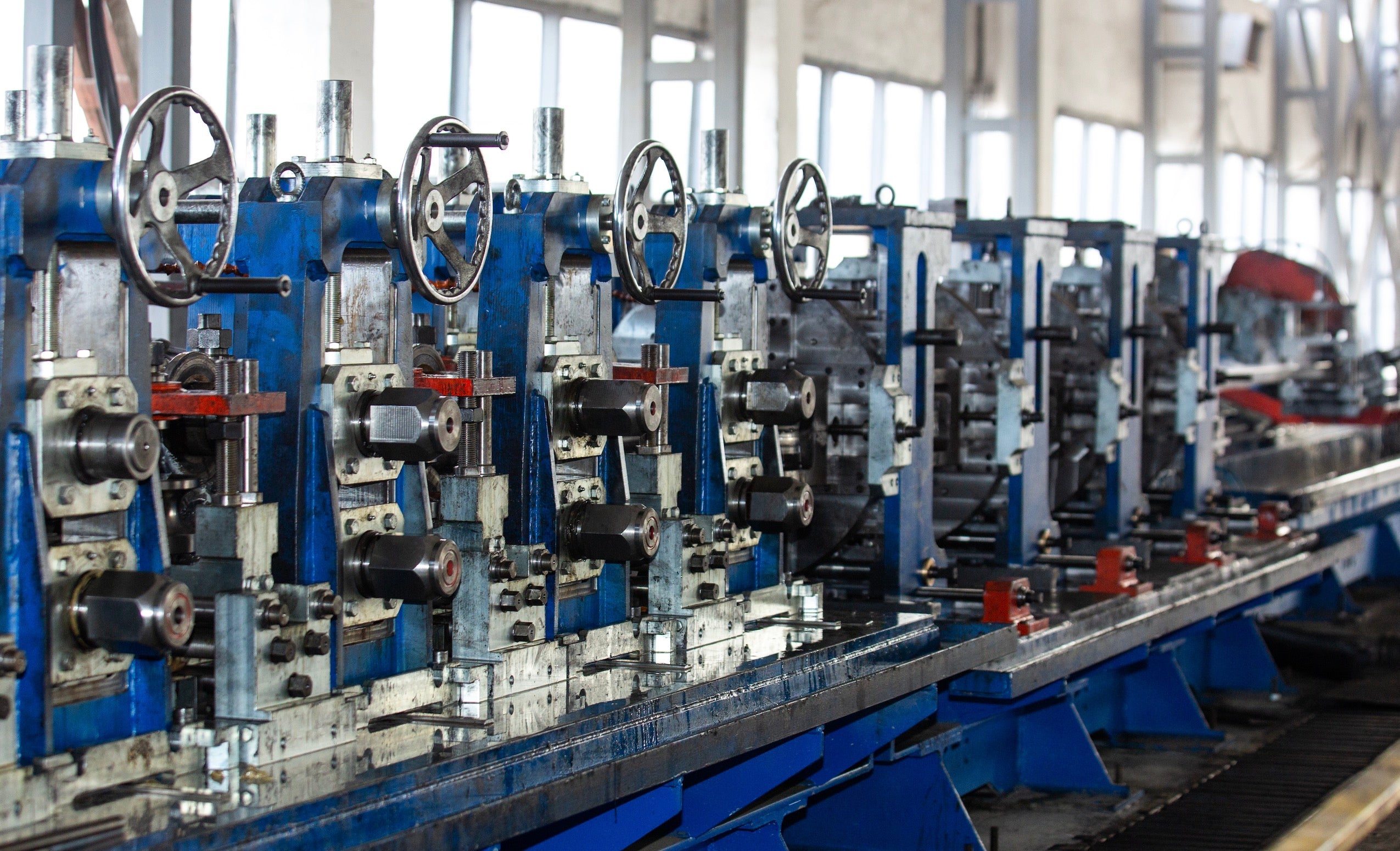
Compensation Plan
To protect our clients' interests, we have established a comprehensive quality compensation policy, especially suitable for B2C clients who cannot directly inspect the goods. Our compensation policy covers issues ranging from product quality defects and shipping errors to potential damages during transit. If the received products have quality issues or do not meet agreed specifications, we will provide appropriate compensation based on the severity of the problem, including refunds, replacement products, or discount compensation. Through this system, we ensure that clients receive reliable assurance and a worry-free service experience, even without direct access to the goods.
Digitalization Gives Us Vitality
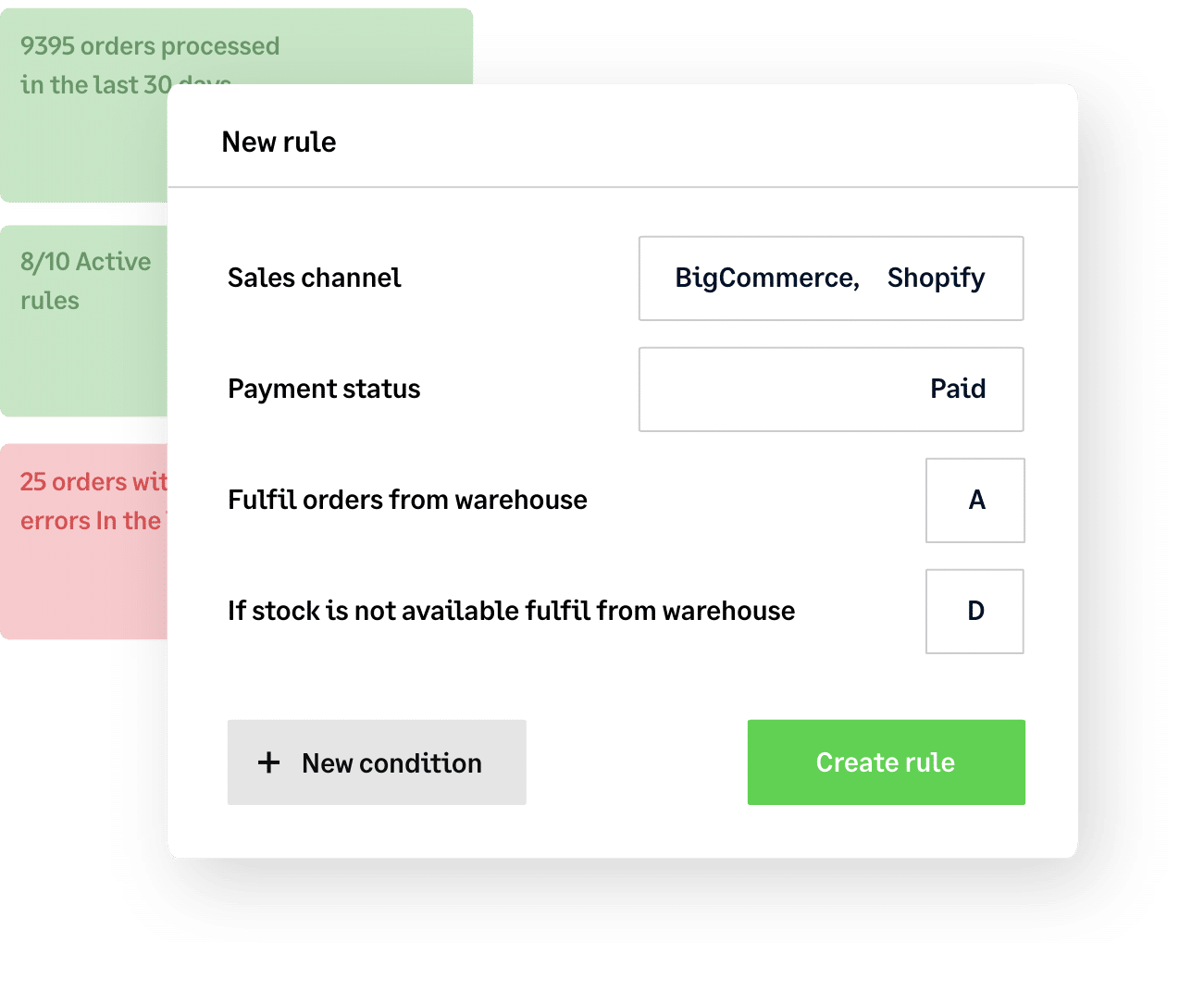
Data-Driven Quality Control
Our quality control system adopts a data-driven approach, collecting key data at every stage of production and inspection to ensure real-time monitoring and optimization of product quality. We use advanced data collection tools to record and analyze details regarding product consistency, acceptance rates, and defect causes, enabling us to identify potential quality issues and trends. Through in-depth analysis of this data, we can quickly detect anomalies and make proactive adjustments, thereby reducing defect rates and substandard products.

Finished product warehousing and traceability management.
Our finished product warehousing and traceability management system ensures that each product is effectively monitored before warehousing and throughout the entire supply chain. Before entering the warehouse, finished products undergo strict final inspection to ensure they meet client requirements in terms of packaging, quality, and compliance.